Yay! Most tools arrived. Check it out! Its like Christmas again...
First up, back rivet plate, flexible lightweight air hose, and maroon scotch write pads. Then air hose is really nice. I'm glad I got it. Definitely would recommend picking one up if you haven't got one yet.
Filing kit (VERY NICE!) 24" ruler, RV-10 Elevator bucking bar, 12" drill bit (looks like #30 is pictured.
The brush is I believe to clean the files..
Tungsten bucking bar, 3X rivet gun, flush set, drill bits, quick change chuck and kit, sioux 6000RPM drill (VERY nice, small, lightweight), assorted rivet sets.
Cleco 1" clamps, Cleco .5" clamps, step drill bit, reamers, mini scotch write wheels, and more....
Fluting pliers, Medium scotch write wheel, fine scotch bright wheel, seamer, countersink cage x2, and more...
So yes, got many tools in. Finally the tools are in. Now I can get a move on the build. But first, I need to learn to use the new tools. More specifically, the ones that can cause more permanent damage. Waiting on the 2 practice kits from Vans Aircraft. Stay tuned.... more to come.
This blog was created to document the adventure of building a Vans RV-10 Experimental Airplane in my garage. It serves as proof that I built it as required by the FAA.
Tuesday, May 31, 2016
Monday, May 30, 2016
Another day without the REST of the TOOLS....
Picked up a HVLP gun at Harbor Freight for 13 bucks. It's shipped with the needle with some sort of grease. Pulled the needle out, cleaned it with mineral spirits. Ran some 50/50 mineral spirits and water through the gun to clean out any thing else it may have that I couldn't reach with the tiny brush cleaner it came with. I also ran acetone thru it to clean it up more and have it dry quickly. Next...Need to wait for the TOOL KIT to ARRIVE so use the scotch brite pads to scuff up the elevators to prime with AKZO to move one to final assembly.
Throughout the day, I skipped around in the plans minus the empennage attachment section and fabricated all the pieces minus deburring. Thats the pile of parts completed today. I couldn't find anything else to make or do so this was the last of the work until the tools arrive.
This is my first mistake! I cut ALL the tail cone J-channels incorrectly. The J-channel in front is cut incorrectly. The one behind is curt correctly. This really took a toll on me. But mistakes happen and I will learn from this for sure. Check and check, and check 5 more times before you cut. Minor detail but still it's wrong. I was able to use all the long (already cut wrong) J-channels and repurpose them for the shorter J-channels called out in the plans. I'll call vans in the morning and order new 8' j-channels.
This is the correct cut, straight on the flat part, 45 degree not the J
Thats it for now till the tools arrive.....lol
Sunday, May 29, 2016
Still waiting on tools. Its Sunday and no one is delivering today. Not UPS, not FedEX, not USPS, NO ONE. Oh well, I'll skip ahead on the plans and work on something else to make my time productive.
Picked up 3 hinges and a 2"X8"X 8' that the store cut in half for me. I could have made the cut at home but didn't wan't to whip out, setup the saw and make a mess for just one cut. Since I was in the sedan, it was easier to transport too, in the trunk.
Made a home made break per the plans. I put in the trim tab and bam, it was bent further. Not sure why its not bent to it's final angle from factory but oh well, done deal. I'll set the break aside in case someone wants to borrow it or till the next build....huh???lol. Oh did I mention I have been loving the build process so far. Totally up my alley.
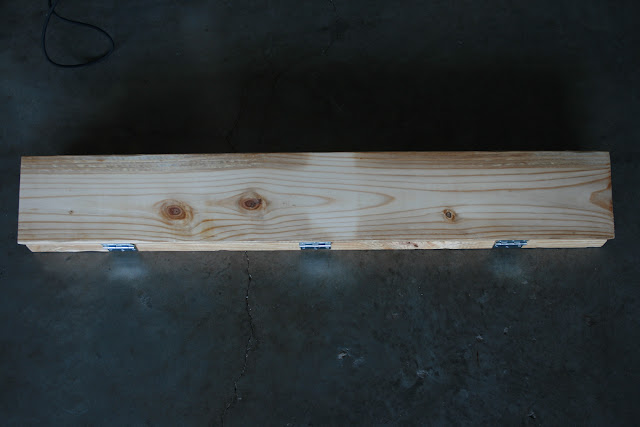
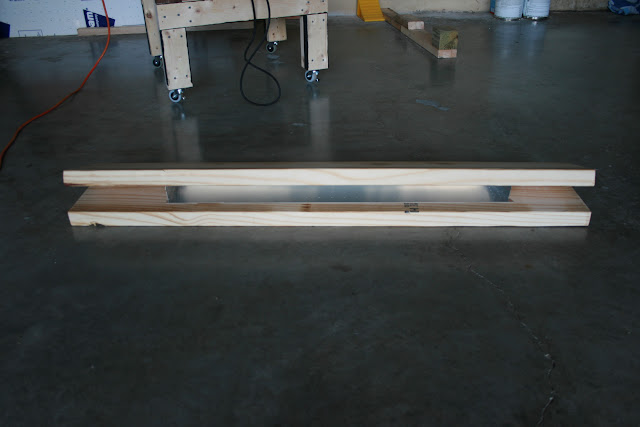
Next up was to bend down the trim tab "tabs". I clamped the skin tight with a c-clamp using wood to protect the skin. I used a 1/2" scrap piece of plywood about 4" long 2" wide and went at it with a hammer. I layed the end of the plywood on top of the tab and hit the wood with the hammer firmly. Not blasting away at it but firmly. As the tab began to bend, the plywood just followed the angle till it was at the desired 90 degree bend.
I used 2 clamps to ensure the skin didn't move. I did all 8 tabs this way. Easy peasy.
Next, I cut the elevator counter balance weights. The band saw made quick work of this task. Since lead can be nasty, I dawned the safety glasses and respirator.
Yup, thats me. Glad I had the safety gear on, The lead was everywhere despite the vacuum connected to the band saw.
Saturday, May 28, 2016
After spending all morning and most of the afternoon building 2 more tables, I had to put in some time in fabricating airplane parts. After all, this is about building an airplane right!
Trim Tab Horn
Removed the shaded area using the band saw. Still need to debur, waiting on scotch bright wheel.
Still waiting on the bulk of the tools and with nothing to do left on the elevators or elevator trim tabs, started looking over the tail cone section. Searched for small band saw related work or stuff I could do with the tools already on hand.
Tables
After clecoing together the elevators I quickly found out I needed more workbench space. Having the right elevator on a wobbly folding table didn't feel right. The foldout table was very narrow having just enough space for the elevator.
Built a 2nd EAA style work bench, added the shelf to the bottom of both EAA tables.
Built a rolling power tool worktable EAA style. Dimensions on the top is 28" long by 21" wide. Also with a shelf at the bottom. This will house the drill press, vise, band saw, and bench grinder. All the power cords were routed neatly with zip ties to the side then underneath to a 14ga 2ft 3 plug extension. 2 of the 4 wheels have brakes. The wheels make is ver easy to move around. This freed up the tool bench top. Oh made of 75% wood laying around from other projects as you can tell from the semi painted parts.
A Few More Tools
Still Waiting on the shipment of the main tool set. While going through the elevator section, I realized a small ruler would be nice to have. Flipping through the cone section, an angle finder would be nice to have to match up the angles on the band saw. Picked them up from the local hardware store and used them right away. The main tool kit will come with a 24" ruler. The 6" will be nicer for shorter measurements. It can measure down to 1/64ths.
The CDI 20-150 in-lb torque wrench came in today via USPS on Saturday. Love it when packages come in the mail. The excitement never goes away to open up a package even thought I know whats inside, lol.
Friday, May 27, 2016
Updates on Vertical Stab
The blue stuff I found around some of the rivets was blue tape put on the flat rivet set to prevent marring of the skins. So that is a non issue now.
Next, this is the email reply from vans regarding the rear spar cap doubler:
This gap looks to me like they missed a step in dimpling/countersinking and you may possibly have a dimple sitting on a flat piece to create this gap. It could also just simply be that when this part was match drilled to the spar it was not clamped tight against the flange. Either way this is not a very desirable situation. I would recommend you dismantle and fix.SterlingVan's Aircraft
I'll drill out the left side of the spar cap to make sure there are dimples. Next I'll put plenty of clamps down to keep the cap flush to the spar then rivet. I'll put this on hold for now until I have some experience under my belt with drilling out rivets.
Elevator Trim Tabs
After work today, I had my first helpers of the project. The elevator skins needed more clecos...
Next we photo copied the trim tab rib cutout.
Carmella cut the rectangles out. I had some 3m headliner spray glue on hand that we used to glue the templates to the foam.
Next I used the band saw to cut out the 6 trim tab ribs. This is the first time using the band saw. Easy peasy.
My wonderful wife came in and snapped a picture of us pulling the blue plastic off the trip tabs. She really came out when we were going to bed. It was 2330. I smiled and said...."Soon..."
The miter saw in the background is from cutting up 2X4 scrap wood to build more work benches. Had to use a foldout table for the miter saw which was ok (wobbly) for the quick job. Ran out of wood so the next morning we picked up more 2X4 and I finished the new work benches.
Thursday, May 26, 2016
Elevators
The previous builder started on the elevators and some parts were already riveted. The tips were riveted, nut plates on one trim doubler were riveted and the control horns were riveted to the front spar. The plans were marked as to what steps were completed but decided to start from the beginning to double check it all for my peace of mind. Since today felt like Christmas in May I had to use the clecos to put some parts together.
First was to cut this ribs then celco. They were already cut, deburred, match drilled, and numbered to include left or right.
Next, The elevator ribs get clecoed to the front and rear spars and bottom skin. All ribs, skins, and spars were previously matched drilled, deburred, and dimpled.
Wow that picture is dark. The garage is stadium bright which doesn't show in the picture. Any suggestions anyone? There a 4 Lithonia LED 4000k 4 ft fixtures in the double car garage. Each fixture has 2 LED stips in them.
After this picture, the shear clips when in then I called it a night at 2330. I was still running on excitement with this first assembly. I'm sure the tail cone wont go this fast. The elevators went together quick since most of the work had already been done. Just going through the process of making sure all parts are accounted for and all steps were completed. Although some parts were already riveted (elevator tip assembly, control horn to forward spar, and right trim nut plates), I plan to prime it as is . Everything else except elevators was primed by previous builder.
Amazing how strong and stiff these parts get once clecoed together. Certainly developing the grip of death.
More Tools....
Its Christmas in May. After work, I stopped by the local hardware store and picked up a band saw and drill press before heading home. At home I was greeted with two boxes. In the boxes were the 1000 silver clecos, 400 copper clecos, and AKZO 2 part epoxy primer. Earlier in the week, the partial face respirator with organic filters and sealed eye protection also arrived.
Need to get organized...
Wednesday, May 25, 2016
Vertical Stab
After reading the pertinent information in the first 5 sections of the manual, it was time to go through the work of the previous builder. Although just looking at the rudder as a newbie builder, its a work of art. Work of art doesn't mean its airworthy though, it is, after all, a critical flight control surface. Everything in this kit will be scrutinized to the best of my ability using the plans, Vans, and VAF until I deem it airworthy.
Right off the bat (and really hard to see in the picture) seems some rivets were set with the blue plastic on. On some of the rivets, there are blue specs underneath the rivets. hmmm... The problem with this is these rivets are not only on the top and bottom ribs, but also the middle ribs. So this skin may have to be completely removed or at least ether the top or bottom rib (depending on the which way the middle rib flange faces) in order get to the middle rivets.
The next area of concern is the left spar cap to rear spar. The right side does not have a gap but left does as you can see in the picture. Seems like the previous builder might not have put on sufficient camps on to hold it flush to the rear spar riveting.
The gap is small but nonetheless present. I will shoot off an email to Vans with this post to get their advise.
There are 3 holes riveted on the rear spar doubler that were supposed to be left open. I have added this to the to do list to remember to drill out before empennage assembly.
That's about all the issues I have seen with the vertical stabilizer.
Tuesday, May 24, 2016
Cracked Open The RV-10 Manual
While waiting for tools to be shipped, I started to read the build manual. Nearly half the manual is purely informational. Whew! Lots of information for sure. There is a steep learning curve going on right now. I don't learn very well by just reading. Reading this ten times will hopefully help this section sink in. Although empennage is partially complete (not by me), all the information is still very important. Unfortunately for me, I'll be starting on the empennage midway thru. No pressure...
For the last few days, I have been reading a few pages before and after work. Trying to get my head into the metal building workflow. So far the rivet sizing seems the most difficult part. I don't remember a digital caliper in the tool kit order. A few pages at a time is a good pace to not overload myself. As of today, the bulk of the tools have not shipped. So I have at least a week to keep reading. Not having tools yet is good for me. I'm a very hands on person and would hate to try something right off the bat and need to order parts cause I buggered up something because I did not read the entire Pre-build info section. I think this is a good time to order some practice kits from the mothership.
Monday, May 23, 2016
Light It Up
Picked up 2 more 4 ft lithonia LED lights for the garage ahem....aircraft factory. Wired them up and and once again, done on a cinch. Okay, so it took about an hour. With four 4' Lithonia LED (dual strip in each fixture) 4000k on the cieling, it really brightens the garage up like a stadium. Wow! I would highly recommend these LED for any garage or shop. For comparison, the Lithonias replaced two 4 ft Phillips with 2 T8s in each. The Lithonias are easily 4X brighter in my opinion. Highly recommended upgrade to any shop garage wheather your building an RV-X or not. Why wouldn't you be building anyway??? Lol.
Sunday, May 22, 2016
Tooling up
Ordered tools 2 nights ago in anticipation of picking up the partially completed empennage. After much research on VAF, the big tool order was placed with Cleaveland Tool. I tried to make sure all the tools needed to be build the complete airplane will be on this order. Many people on the forums though say "your never done buying tools". It was a big chunk of change at nearly the cost of the RV-10 empennage kit from VANS directly.
I also ordered 2 part epoxy primer AKZO, a partial face respirator with organic filters, and eye protection.
I also added 2 4ft Lithonia LED 4000k lights from the local aircraft hardware store. Need to get 2 more to replace the old dying florecents that barely put out any light. These new LED are AMAZING! WOW. They really brightend up the gargae ALOT. There is still 2 dark spots that I think will resolve themselves when replacing the 2 old fixtures. Wiring was a cinch and very quick. Had the lights up and running in less than 1 hour. May put a dimmer on them for the times i'm not needing all the exra light.
Picking Up the Empennage
After some planning througout the week, the day has come to pick up the FIRST kit of the airplane, the empennage. The empennage is the "aft" or back part of the airplane that includes the taile cone, horizontal stabilizer, elevators, vertical stabilizer, and rudder. The rudder, vertical stabilizer and horizontal stabilizers are complete. The elevators were started but no riviting was done to them yet.
My son Manny and I woke up bright and early at 0530. We loaded up the VW Jetta with the horizontal stabilizer cradles built earlier in the week, gobs of tiedown straps, a cordless drill, and patio pillows. With the fuel gauge needle hovering on the "E" mark, we made a quick stop at the fuel station to top off with diesel. After the top off, we headed on the Floridas turnpike in search of I-95. Traffic was nearly nonexistent at this early in the morning at 0600. Before we knew it, we were in Winter Springs, FL in no time.
We met with Roy at his beautiful property with a separte motor home sized garage/shop. He took the time to show us his nice work and some mishaps which I gladly appreciated. We looked over all the asembled parts closely and were happy not to find anything that popped out as unusual (for a newbie builder at least). The bulk of the parts small to medium parts were in a waist high cardboard box. The very small parts (rivtis, bolts, nuts, etc.) were in their original Vans packaging or in appropriately sized tupperware type containters. He offered to do a full parts inventory but with time contraints and parts already assembled, I didn't think that was really feasible.
With the purchase certain now, we jumped back in the trusty VW and headed up the road some 5 miles to what looked like a an auto wrecker shop. I was close, it was an auto mechanic shop but WOW, what a dump. Singed the paperwork for the 15' box rental truck and the fuel gauge didn't match the paperwork. They gave me the paperwork for a different truck. Fixed the paperwork and Manny drove the VW and I the box truck back to Roys house.
We loaded the all the parts very carefully over the next 1.5 hours. The patio pillows came in very handy. I also rented 24 moving blankets which were essential to protect the all the parts. Large skins were placed on the floor with 2 blankets in between each blanket. Rudder and vertical stabilizer were padded with several layers of blankets and secured to the side using the rails. The horizontal stabilizer was set into the cradle and also secured to the rails with straps.
The ride home with uneventful with a quick pit stop for fuel, food, and empty bladders. We unloaded the truck into the garage in no time flat. Returned the truck at a local place and made a stop at the local aircraft hardware shop for supplies. We built a ceiling hanging shelve out of 2X2 and lamp chain rated for 90 lbs. The rudder, vertical stabilizer, and horizontal stabilizer with 1/2" foam all went up there easily and out of the way. All other skins went on to a top shelf also up and out of the way.
Still need to organize the small parts, and the waist high box full of parts as well.
Thats it for now. Took plenty of pictures but cant post them up just yet. Stay tuned for more....
After some planning througout the week, the day has come to pick up the FIRST kit of the airplane, the empennage. The empennage is the "aft" or back part of the airplane that includes the taile cone, horizontal stabilizer, elevators, vertical stabilizer, and rudder. The rudder, vertical stabilizer and horizontal stabilizers are complete. The elevators were started but no riviting was done to them yet.
My son Manny and I woke up bright and early at 0530. We loaded up the VW Jetta with the horizontal stabilizer cradles built earlier in the week, gobs of tiedown straps, a cordless drill, and patio pillows. With the fuel gauge needle hovering on the "E" mark, we made a quick stop at the fuel station to top off with diesel. After the top off, we headed on the Floridas turnpike in search of I-95. Traffic was nearly nonexistent at this early in the morning at 0600. Before we knew it, we were in Winter Springs, FL in no time.
We met with Roy at his beautiful property with a separte motor home sized garage/shop. He took the time to show us his nice work and some mishaps which I gladly appreciated. We looked over all the asembled parts closely and were happy not to find anything that popped out as unusual (for a newbie builder at least). The bulk of the parts small to medium parts were in a waist high cardboard box. The very small parts (rivtis, bolts, nuts, etc.) were in their original Vans packaging or in appropriately sized tupperware type containters. He offered to do a full parts inventory but with time contraints and parts already assembled, I didn't think that was really feasible.
With the purchase certain now, we jumped back in the trusty VW and headed up the road some 5 miles to what looked like a an auto wrecker shop. I was close, it was an auto mechanic shop but WOW, what a dump. Singed the paperwork for the 15' box rental truck and the fuel gauge didn't match the paperwork. They gave me the paperwork for a different truck. Fixed the paperwork and Manny drove the VW and I the box truck back to Roys house.
We loaded the all the parts very carefully over the next 1.5 hours. The patio pillows came in very handy. I also rented 24 moving blankets which were essential to protect the all the parts. Large skins were placed on the floor with 2 blankets in between each blanket. Rudder and vertical stabilizer were padded with several layers of blankets and secured to the side using the rails. The horizontal stabilizer was set into the cradle and also secured to the rails with straps.
The ride home with uneventful with a quick pit stop for fuel, food, and empty bladders. We unloaded the truck into the garage in no time flat. Returned the truck at a local place and made a stop at the local aircraft hardware shop for supplies. We built a ceiling hanging shelve out of 2X2 and lamp chain rated for 90 lbs. The rudder, vertical stabilizer, and horizontal stabilizer with 1/2" foam all went up there easily and out of the way. All other skins went on to a top shelf also up and out of the way.
Still need to organize the small parts, and the waist high box full of parts as well.
Thats it for now. Took plenty of pictures but cant post them up just yet. Stay tuned for more....
Wednesday, May 18, 2016
Killer Deal
I have been working 60-80 hours a week to quickly save up for tools and empennage kits. During downtime, sneak over to VAF. The classified section received close attention for tools. Well, a partially complete (rudder, vertical stab, horizontal stab complete; elevator started) empennage kit was for sale only 2 hours away in Orlando Florida for $1000!!! I INSTANTLY replied and got in touch with the seller Roy. He sent me about 140 pictures that night, and we agreed on the following weekend to meet up. Thank you Roy!! This certainly saved money that will not be put toward the wing kit, but also saved a bunch of build time.
Today after work, built 4 horizontal stabilizer cradles out of some scrap wood. Remember that fish tank that was scrapped, yup, still reusing the wood. The H. Stab will be the longest piece to transport at a bit more than 11 feet long. After some searching online, and texting with Roy, I got the measurements for the H. Stab to build the cradles in advance.
2X4 wood already cut.
Found the Center and measured 2.5" to each side. I marked 4.5 but it's actually 5". The H. Stab is about 4 inches thick. Added 1" for a bit extra room.
The inside of the vertical 2X4s, are lined up with the above marks then held in place with standard wood screws.
Meet my little friend hanging out in the cradle hall.
A total of 4 built
Some regular 1" ratchet strap laying around
And here it is. Cradles made with nothing but supplies already on hand.
Yup, I need better lighting in the garage. Looks like I'll have to install the lighting sooner than later.
Stay tuned for more...
Monday, May 9, 2016
EAA Workbench
Since I did not have much to do at home today, I thought building an EAA workbench was a good RV motivational task. Last year I scrapped a 10 ft wide by 2.5ft wide by 5 ft high fish tank breeding rack from the garage. It left me with tons of 2X4 and plywood. Pulled out the miter saw and set it up in the side yard out the side garage door to keep the saw dust out. After a couple hours, I had myself an EAA work bench at no cost. Still need to rip more plywood for the bottom shelf. That will be left for another RV motivational task in the future.
standard EAA work bench
Picture is a bit dark, sorry about that. Garage lighting sure does need to be upped. That will be for another day. As usual, stay tuned...
Here is the link for the EAA workbench.
A Bit More Progress
Today I received my first order specifically for the RV-10 build. Its the Aircraft Structural Technician Book by Dale Hurst. Amazon had the best price shipped to my door. Being a Prime member, it arrived in 2 days (no shipping charge).
Spend a few days deciding on which tools to get. Searching the VAF forums and builder websites, I have come up with a list of tools I plan to purchase from Cleveland Aircraft Tools (CAT) with the exception of the clecos. The clecos will come from Brown Tool due to a saving of $200 over CAT. Although I'll have plenty of time to finish the build (10 years?) the nice to have tools will be on the list. For instance, pneumatic squeezer, 1000 3/32 clecos, quick change chuck kit for drill, DRDT-2, multiple different yokes, 2 countersink cages, yoke quick change pins, and more. I'm a tool person. My wife taught me the importance of having the right tool for the job. I remember the days when we were staining our new wooden fence. Took 2 hours to do one 8 ft panel. She took off to Home Depot and came back with a power sprayer. One panel took 2 min or less with the right tool! Ever since then, I usually splurge for the right tool. The results and time savings speak for themselves.
Once the aircraft tools arrive, they will have a nice home on the right wall. Tools stuffed in draws get lost or forgotten. I believe in easy access and easy to see tool storage. This tool storage method makes for minimal time loss when using them.
Thats it for now.. For now, I'll read the book to keep me busy. Stay tuned.
Also, I bolted the air compressor air hose reel to the concrete block. This needed to be done a long time ago. So much easier to reel up the hose now...
26 gallon belt driven Campbell Compressor.
Spend a few days deciding on which tools to get. Searching the VAF forums and builder websites, I have come up with a list of tools I plan to purchase from Cleveland Aircraft Tools (CAT) with the exception of the clecos. The clecos will come from Brown Tool due to a saving of $200 over CAT. Although I'll have plenty of time to finish the build (10 years?) the nice to have tools will be on the list. For instance, pneumatic squeezer, 1000 3/32 clecos, quick change chuck kit for drill, DRDT-2, multiple different yokes, 2 countersink cages, yoke quick change pins, and more. I'm a tool person. My wife taught me the importance of having the right tool for the job. I remember the days when we were staining our new wooden fence. Took 2 hours to do one 8 ft panel. She took off to Home Depot and came back with a power sprayer. One panel took 2 min or less with the right tool! Ever since then, I usually splurge for the right tool. The results and time savings speak for themselves.
current work bench setup
Once the aircraft tools arrive, they will have a nice home on the right wall. Tools stuffed in draws get lost or forgotten. I believe in easy access and easy to see tool storage. This tool storage method makes for minimal time loss when using them.
Thats it for now.. For now, I'll read the book to keep me busy. Stay tuned.
Subscribe to:
Posts (Atom)